Overview
Each of the six power generating units has a capacity of 660MW when burning coal, giving a total capacity of just under 4,000MW, making this the largest power station, producing 10% of the UK’s power.
In 2015-16, the Power Station underwent an upgrade of the Continuous Emissions Monitoring Systems (CEMS) for both their coal and biomass power generating units to comply with the Industrial Emissions Directive (IED).
CEM systems are housed on all six of the power generating units plus three CEM systems are installed in existing housings to monitor the Flue Gas Desulphurisation (FGD) process on the three coal fired generators.
a1-cbiss had previously gained the sites’ trust whilst successfully developing a data acquisition software package for the site. So in 2015, a1-cbiss Ltd were selected as the supplier of choice based on their excellent reputation and industry experience in developing bespoke CEM system projects and delivering the full hardware package.
The Challenges
- Space Limit: There is only one flue stack which emits emissions to atmosphere. Of which, all six power generating units require a duct within the stack.
One of the biggest challenges was to house all six CEM systems within each power generating unit near to the stack using the minimum amount of space.
Each CEM system typically requires:
- A sample probe
- Filters
- A sample line (umbilical)
- A gas conditioning system
- A calibration gas system
- Housing to accommodate the 19” rack gas analyser and 19” rack dual redundancy gas analyser
- Logistics of the fluidics, control, power, instrumentation, software and transportation of the redundancy system
Because of the limited space, the chimney was unable to accommodate such systems and therefore required a complete re-design of this typical system.
- Permit Requirements: Under the Industrial Emissions Directive (IED), sites are required to reduce Oxides of Nitrogen (NOX) emissions from biomass, waste and coal. The Power Station therefore, required a CEM system upgrade to monitor the Ammonia (NH3) slip using Selective Non-Catalytic Reduction (SNCR).
New analysers should be certified, for a suitable measurement range, under the Environment Agency’s MCERTS scheme. The means of assessing the suitability of the CEM system determines that the certification range must be less than 2.5 times the Emission Limit Value (ELV).
- Redundancy System: Each of the six power generating units required two duty sets of gas analysers. Additional to this, rather than have separate 37U 19” rack standby systems for each duty, a single half sized standby redundancy system that was portable between each of the duty systems was developed.
- Cost: Due to the sheer size of the power plant, one of the challenges was to make cost savings where possible in the engineering of the CEM systems.
The Solution
- Space Limit Solutions: Fitting so much equipment in half size enclosures was only the beginning of the challenge. a1-cbiss were called upon to write a new design for the 19” gas analyser rack.
Together with the complexity of the customers’ needs, the design team at a1-cbiss had to think outside the box and completely re-design the systems that would normally be produced.
The whole system was uniquely designed to allow two individual gas analysers and ancillaries to be combined into a single 19” rack, positioned in each of the six housings.
The six shelters had to be uniformly positioned on site near to the flue stack whilst considering the heated line lengths and power cables to reduce sample lag and also to reduce costs.
- Permit Requirements: For the plant to adhere to their emissions monitoring site permit and accurately measure all of the gases specified including Ammonia, a1-cbiss selected the MIR-FT gas analysers.
The MCERTS certified MIR-FT multi gas analyser, installed on over 1500 sites worldwide, was chosen because of its capability for measuring the specified ranges to meet the requirements of IED and EN14181.
- Redundancy System: A portable standby redundancy CEM system was also designed to be interchangeable between the six systems that enabled the customer to integrate the portable standby system quickly and easily using hot-swappable ports which prevented any loss of sample, pressure or heat.
In order to achieve the specification of a portable standby system, the design team developed an interconnections panel using a number of plug and socket combinations for not only electrical power, but also for signals, communications including the ability to connect to existing site communication networks, and fluidics, such as compressed air and gases.
The complexity of the emissions monitoring setup required a1-cbiss to design the system to comply with existing site electrical architecture. This included the development of transformers with design of 400v AC and 110v AC supply monitoring change over panels to ensure the system was able to cope with the sites fluctuations in power.
The redundancy system is always switched on and ready so that in the event where a duty system has a problem, it can be used straightaway without having to be powered and warmed up.
In addition to the CEM system hardware, the design team liaised closely with the software department to re-engineer the signal transfer to the data acquisition software (CDAS) which enabled the flexibility of a portable standby system to be connected, calibrated and maintained so that the Quality Assurance Level (QAL) 3 requirements for EN14181 could be achieved.
4. Cost: Thanks to the effective design which was made possible by the a1-cbiss design engineers, it resulted in a huge costing saving. A single rack system reduced hardware costs.
The portable redundancy unit saved the plant from having to invest in a redundancy unit for each of the housings.
Conclusion
To illustrate the magnitude of this project, almost 1,000 drawings were delivered by a team of 4 design engineers as part of the engineering team which involved over 30 individuals.
a1-cbiss were hugely influential in the initial CEMS concept and worked closely with the customer to develop a future proof system that not only works with today’s systems, but tomorrow’s systems too.
There were numerous challenges to overcome in order to meet the specifications set out by the Power Station, and the requirements of integrating the new systems with the 42 year old site.
The design team developed a working solution around the core beginnings of a1-cbiss to provide Custom Built Intelligent Sampling Systems.
Overall, the project took a lot of ingenuity, experience, knowledge and understanding from the design team, particularly regarding legislative acts. “A professional outstanding design team, worked excellently together and far exceeded the requirements of this project” commented the Power Plant Manager.
The ideas learnt and developed through the project have enabled a1-cbiss to evolve with new and impressive technology. These concepts will support future projects for customers that require solutions to demanding engineering challenges.
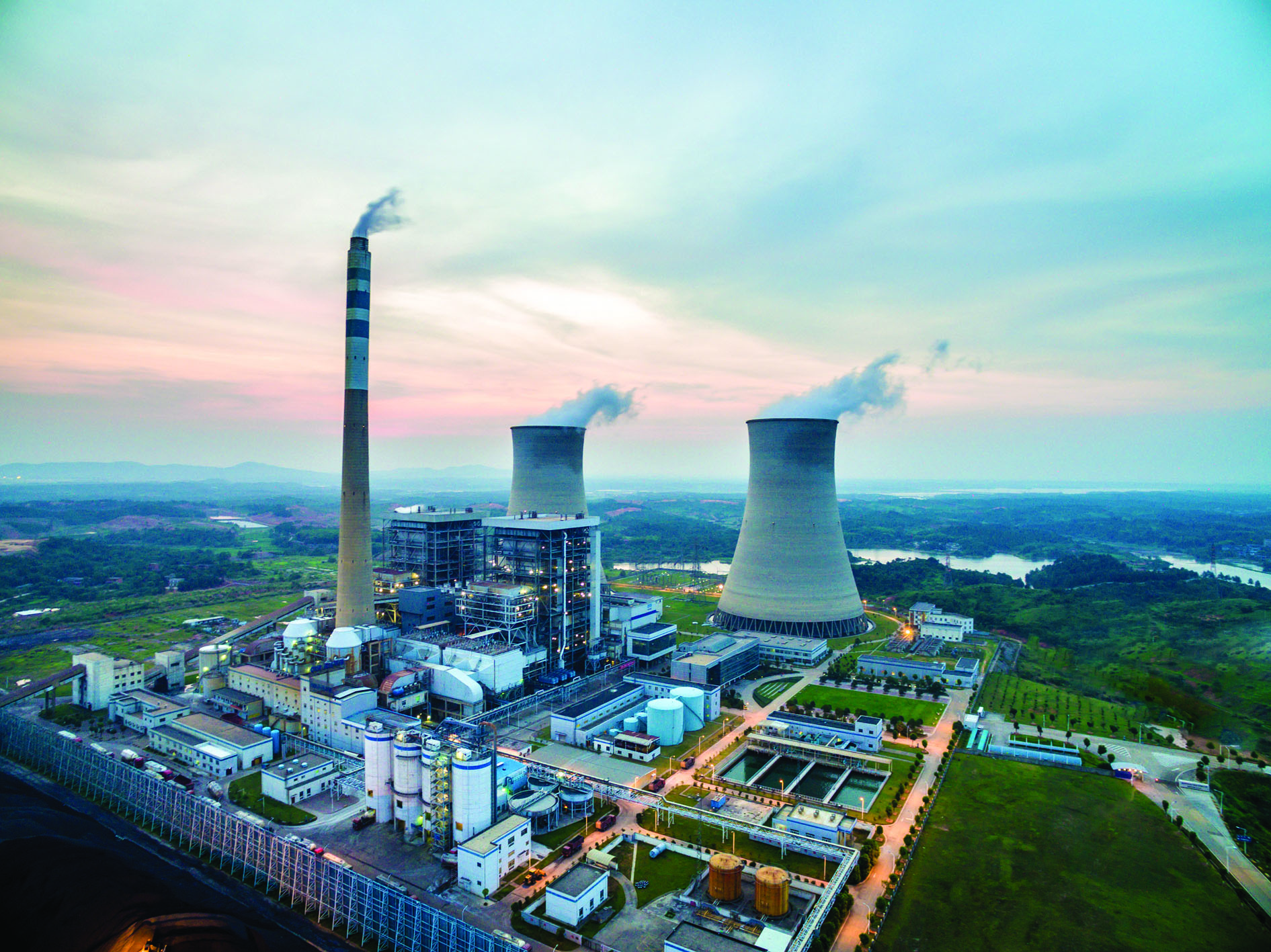
Talk with the Experts
Contact us - Our team of application specialists can assist you with system design, installation, maintenance, and repair. As a systems integrator, we provide end-to-end support to ensure your facility has a reliable and effective gas detection system in place.
Sign up for more information - For more information on protecting your staff from the dangers of gas leaks, sign up for our emails.